Predictive Maintenance
Core Fundamentals
Predictive maintenance transforms traditional maintenance approaches by shifting from time-based or failure-based maintenance to condition-based maintenance that responds to actual equipment health indicators. This methodology relies on continuous monitoring of equipment parameters including vibration, temperature, pressure, electrical signatures, and operational performance metrics to identify patterns that precede failures.
The approach leverages historical failure data, real-time sensor information, and advanced analytics to create predictive models that can forecast equipment degradation and remaining useful life. These models enable maintenance teams to schedule interventions at optimal times that maximize equipment availability while minimizing maintenance costs and safety risks.
Modern predictive maintenance systems integrate with enterprise maintenance management systems to automate work order generation, resource planning, and maintenance scheduling based on predicted failure probabilities and operational priorities.
Key Technologies and Components
Predictive maintenance implementations typically comprise several interconnected technologies:
- Condition Monitoring: Continuous surveillance of equipment parameters through sensors and monitoring systems
- Data Analytics: Advanced algorithms including statistical analysis, machine learning, and artificial intelligence
- Predictive Models: Mathematical models that forecast equipment behavior and failure probabilities
- Maintenance Management: Integration with enterprise systems for work order generation and resource planning
- Visualization Tools: Dashboards and reporting systems that present equipment health and maintenance recommendations
- Mobile Applications: Field-ready tools that enable maintenance technicians to access predictions and update system information
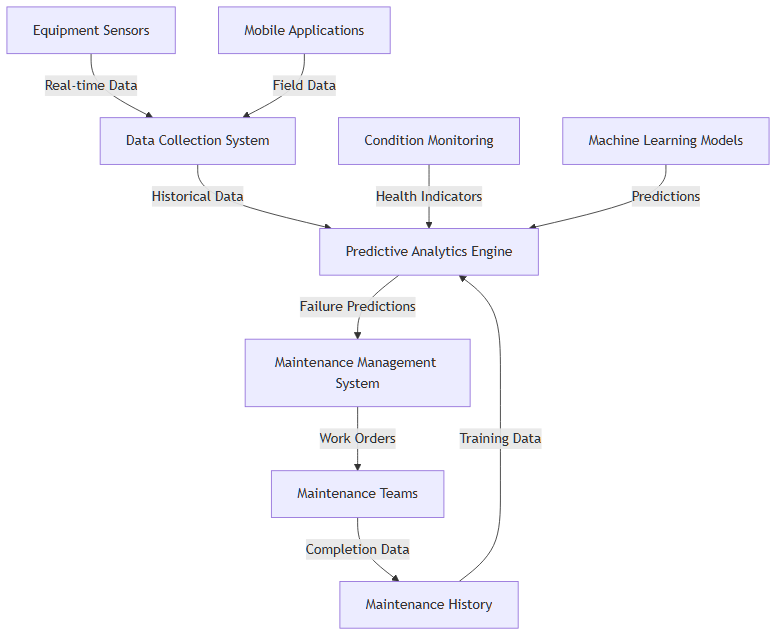
Applications and Use Cases
Rotating Equipment Monitoring
Predictive maintenance provides significant value for rotating equipment including motors, pumps, compressors, and turbines. Vibration analysis, oil analysis, and thermal monitoring enable early detection of bearing wear, shaft misalignment, and other mechanical issues that can lead to catastrophic failures.
Process Equipment Optimization
Manufacturing process equipment benefits from predictive maintenance through monitoring of process parameters, equipment performance, and product quality indicators. These systems can predict when equipment degradation begins affecting product quality or process efficiency.
Electrical System Monitoring
Electrical equipment including transformers, switchgear, and motor control centers require specialized predictive maintenance approaches that monitor electrical signatures, power quality, and thermal conditions to prevent electrical failures and safety incidents.
Implementation Strategies
Sensor Integration: Successful predictive maintenance requires comprehensive sensor networks that monitor critical equipment parameters. Sensor selection must balance measurement accuracy, reliability, and cost while considering environmental conditions and installation requirements.
Data Infrastructure: Predictive maintenance generates large volumes of data that require scalable storage, processing, and analytics capabilities. Cloud platforms and edge computing solutions provide the infrastructure necessary to handle high-frequency sensor data and complex analytical workloads.
Model Development: Effective predictive models require extensive historical data, domain expertise, and iterative development processes. Model validation using historical failure data ensures accuracy and reliability before deployment in production environments.
Benefits and ROI Considerations
Reduced Downtime: Predictive maintenance enables planned maintenance activities that minimize unplanned downtime and production disruptions. Equipment availability improvements often justify the entire investment in predictive maintenance systems.
Cost Optimization: Condition-based maintenance reduces unnecessary maintenance activities while ensuring critical interventions occur before failures happen. This optimization typically reduces maintenance costs by 10-30% while improving equipment reliability.
Safety Improvements: Early detection of equipment degradation prevents catastrophic failures that could result in safety incidents, environmental releases, or personnel injuries. Risk reduction represents a significant but often unquantified benefit of predictive maintenance programs.
Integration with Industrial Systems
Predictive maintenance integrates closely with digital twin implementations by providing real-time validation of virtual model accuracy and updating model parameters based on actual equipment behavior. Integration with real-time analytics platforms enables immediate response to critical equipment conditions.
The technology leverages anomaly detection algorithms to identify unusual equipment behavior that may indicate impending failures. Time series analysis techniques provide the foundation for trend analysis and failure prediction models.
Technology Platforms and Solutions
Enterprise Platforms: Comprehensive predictive maintenance platforms including GE Predix, Siemens MindSphere, and Schneider Electric EcoStruxure provide integrated solutions that combine data collection, analytics, and maintenance management capabilities.
Cloud Analytics: Cloud-based analytics services including AWS IoT Analytics, Azure IoT Suite, and Google Cloud IoT enable scalable predictive maintenance implementations with pre-built algorithms and visualization tools.
Specialized Solutions: Industry-specific predictive maintenance solutions address unique requirements including regulatory compliance, safety standards, and domain-specific failure modes for industries including oil and gas, power generation, and discrete manufacturing.
Best Practices and Implementation Guidelines
- Start with critical equipment that has high failure impact and sufficient historical data for model development
- Establish baseline performance through comprehensive data collection before implementing predictive algorithms
- Integrate with existing systems including maintenance management, enterprise resource planning, and operational systems
- Provide training and change management to ensure maintenance teams can effectively use predictive maintenance tools
- Implement continuous improvement processes that update models based on new failure data and operational experience
- Monitor system performance through key performance indicators including prediction accuracy, maintenance cost reduction, and equipment availability
Challenges and Considerations
Data Quality: Predictive maintenance accuracy depends heavily on data quality, completeness, and consistency. Poor data quality can lead to incorrect predictions and reduced system effectiveness.
Model Complexity: Balancing model complexity against interpretability and computational requirements represents an ongoing challenge. Complex models may provide better accuracy but require more resources and expertise to maintain.
Organizational Change: Successful predictive maintenance implementation requires significant organizational change including new processes, skills, and cultural acceptance of data-driven decision making.
Related Concepts
Predictive maintenance closely relates to condition monitoring and sensor data processing applications. The technology integrates with industrial data collection systems and unified namespace architectures.
Artificial intelligence and machine learning provide the analytical capabilities that enable accurate failure predictions. Data integration ensures predictive maintenance systems have access to comprehensive operational data necessary for effective analysis.
Predictive maintenance represents a transformative approach to equipment maintenance that enables organizations to optimize asset performance, reduce costs, and improve operational reliability. Success requires careful attention to technology selection, data quality management, and organizational change management to realize the full potential of condition-based maintenance strategies in industrial environments.
What’s a Rich Text element?
The rich text element allows you to create and format headings, paragraphs, blockquotes, images, and video all in one place instead of having to add and format them individually. Just double-click and easily create content.
Static and dynamic content editing
A rich text element can be used with static or dynamic content. For static content, just drop it into any page and begin editing. For dynamic content, add a rich text field to any collection and then connect a rich text element to that field in the settings panel. Voila!
How to customize formatting for each rich text
Headings, paragraphs, blockquotes, figures, images, and figure captions can all be styled after a class is added to the rich text element using the "When inside of" nested selector system.