Event-Driven Architecture (EDA)
Understanding Event-Driven Architecture in Industrial Systems
Event-Driven Architecture transforms traditional request-response industrial systems into reactive systems that respond immediately to operational events as they occur. In manufacturing environments, this means equipment status changes, production milestones, quality measurements, and safety conditions can trigger immediate automated responses without waiting for scheduled polling or batch processing cycles.
The architecture revolves around three fundamental components:
- Event producers generate notifications when significant changes occur in industrial systems
- Event channels provide reliable transport mechanisms for distributing events across the system
- Event consumers respond to events by executing business logic, triggering controls, or updating system states
This approach enables manufacturing systems to operate more responsively, efficiently, and safely by reducing latency between operational events and system responses.
Core Architecture Components
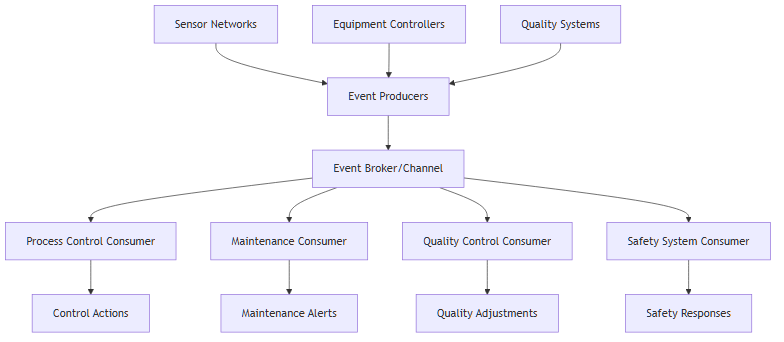
Event Producers in Industrial Systems
Industrial event producers generate notifications based on operational conditions:
Equipment Event Producers:
- Machine status changes (startup, shutdown, fault conditions)
- Performance threshold violations (speed, temperature, pressure limits)
- Maintenance condition indicators (vibration levels, oil quality, wear measurements)
- Safety system activations (emergency stops, guard door openings, alarm conditions)
Process Event Producers:
- Production milestone completion (batch completion, quality gates passed)
- Material flow events (inventory changes, material shortages, quality deviations)
- Environmental condition changes (temperature, humidity, air quality variations)
- Energy consumption events (power consumption spikes, efficiency deviations)
Quality Event Producers:
- Inspection results (pass/fail decisions, measurement deviations)
- Statistical process control (control chart violations, trend detections)
- Customer feedback (quality complaints, return notifications)
- Compliance events (regulatory violations, audit findings)
Event Channels and Message Brokers
The event distribution infrastructure manages reliable event delivery:
Message Broker Technologies:
- Apache Kafka for high-throughput, fault-tolerant event streaming
- MQTT brokers for lightweight IoT device communication
- RabbitMQ for flexible routing and queuing capabilities
- Industrial protocols like OPC UA for standardized industrial communication
Event Channel Characteristics:
- Persistence ensuring events are not lost during system outages
- Partitioning enabling parallel processing of event streams
- Ordering guarantees maintaining event sequence when required
- Scalability handling varying event volumes and consumer loads
Event Consumers and Response Systems
Event consumers implement business logic responding to operational events:
Real-time Control Consumers:
- Process controllers adjusting setpoints based on quality events
- Safety systems implementing protective actions for hazardous conditions
- Energy management optimizing consumption based on production events
- Inventory management triggering material orders based on usage events
Analytics and Monitoring Consumers:
- Performance monitoring calculating real-time operational metrics
- Predictive analytics analyzing patterns for maintenance predictions
- Quality analysis tracking product quality trends and variations
- Compliance monitoring ensuring regulatory requirement adherence
Industrial Implementation Patterns
Stream Processing for Continuous Analysis
Stream processing enables continuous analysis of real-time event flows:
Example: Real-time equipment health monitoring
def process_vibration_events(event_stream):
return (event_stream
.filter(lambda event: event.equipment_type == 'motor')
.window(size=timedelta(minutes=5))
.aggregate(lambda events: {
'avg_vibration': mean([e.vibration for e in events]),
'max_vibration': max([e.vibration for e in events]),
'equipment_id': events[0].equipment_id,
'timestamp': events[-1].timestamp
})
.filter(lambda result: result['max_vibration'] > VIBRATION_THRESHOLD)
.map(lambda result: create_maintenance_alert(result)))
Complex Event Processing (CEP)
CEP enables detection of patterns across multiple event streams:
- Equipment correlation analysis detecting patterns across multiple machines
- Process sequence monitoring ensuring proper manufacturing step completion
- Multi-sensor fusion combining data from different sensor types
- Temporal pattern detection identifying time-based operational patterns
Event Sourcing for Audit and Traceability
Event sourcing maintains complete audit trails for regulatory compliance:
- Production traceability recording all events affecting product quality
- Equipment history maintaining complete operational event records
- Compliance documentation preserving evidence for regulatory audits
- Root cause analysis enabling detailed investigation of operational issues
Benefits for Industrial Operations
Low-Latency Response
EDA enables immediate response to operational conditions:
- Sub-second reaction times for safety-critical events
- Parallel processing of multiple event streams simultaneously
- Reduced coupling between systems enabling faster response
- Event-driven optimization adjusting operations based on real-time conditions
Enhanced Scalability
Event-driven systems scale effectively with operational growth:
- Independent scaling of event producers and consumers
- Distributed processing across multiple computing resources
- Event partitioning enabling parallel processing capabilities
- Cloud integration supporting hybrid on-premises and cloud deployments
Improved System Resilience
EDA provides robust failure handling and recovery:
- Event persistence ensuring no operational data is lost during outages
- Loose coupling preventing cascading failures across systems
- Fault isolation containing problems within individual components
- Event replay enabling system recovery and debugging capabilities
Implementation Challenges and Solutions
Event Schema Design and Evolution
Managing event structure changes over time:
- Schema versioning supporting backward compatibility during system upgrades
- Event validation ensuring data quality and format compliance
- Migration strategies handling schema changes without system downtime
- Documentation maintenance keeping event contracts current and accessible
Performance Optimization
Ensuring EDA systems meet industrial performance requirements:
- Event batching balancing latency with throughput requirements
- Consumer optimization tuning processing logic for efficiency
- Infrastructure scaling provisioning adequate compute and network resources
- Monitoring and profiling identifying and resolving performance bottlenecks
Data Consistency and Ordering
Managing event processing order and consistency:
- Event ordering maintaining sequence when required for process integrity
- Idempotent processing handling duplicate events gracefully
- Eventual consistency managing distributed state across multiple systems
- Conflict resolution handling competing updates from multiple sources
Integration with Industrial Systems
SCADA and HMI Integration
Connecting event-driven systems with operational interfaces:
- Real-time display updates reflecting current operational events
- Alarm management routing critical events to operator stations
- Historical trending incorporating events into process history
- Operator interaction enabling manual responses to automated events
Manufacturing Execution System (MES) Integration
Coordinating with production management systems:
- Production scheduling adjusting schedules based on equipment events
- Quality management integrating inspection and test results
- Material management coordinating inventory and logistics
- Performance tracking calculating real-time operational metrics
Enterprise Resource Planning (ERP) Integration
Connecting operational events with business systems:
- Financial integration recording production costs and efficiency metrics
- Supply chain coordination triggering procurement based on operational events
- Customer communication providing real-time production status updates
- Regulatory reporting aggregating compliance-related events
Best Practices for Industrial EDA Implementation
Event Design and Management
- Design meaningful events that represent significant business or operational changes
- Use consistent event schemas across related systems and applications
- Implement proper event lifecycle management including archival and cleanup
- Maintain event documentation for system integration and troubleshooting
- Version events appropriately to support system evolution and maintenance
System Architecture and Operations
High Availability Design:
- Redundant event brokers preventing single points of failure
- Geographic distribution supporting multi-site manufacturing operations
- Automated failover ensuring continuous operation during component failures
- Regular disaster recovery testing validating system resilience capabilities
Security and Compliance:
- Event encryption protecting sensitive operational information
- Access controls restricting event consumption to authorized systems
- Audit logging maintaining security and compliance records
- Data privacy ensuring personal information protection in event data
Related Concepts
Event-Driven Architecture forms the foundation for many advanced industrial applications including microservices architecture, distributed systems, and real-time analytics platforms. Understanding these relationships is essential for implementing comprehensive industrial automation solutions that can respond effectively to operational events while maintaining the scalability, reliability, and performance standards required for modern manufacturing environments.
What’s a Rich Text element?
The rich text element allows you to create and format headings, paragraphs, blockquotes, images, and video all in one place instead of having to add and format them individually. Just double-click and easily create content.
Static and dynamic content editing
A rich text element can be used with static or dynamic content. For static content, just drop it into any page and begin editing. For dynamic content, add a rich text field to any collection and then connect a rich text element to that field in the settings panel. Voila!
How to customize formatting for each rich text
Headings, paragraphs, blockquotes, figures, images, and figure captions can all be styled after a class is added to the rich text element using the "When inside of" nested selector system.