Data Loss Window
Summary
A Data Loss Window represents the maximum amount of time during which critical industrial data might be lost in case of a system failure, network disruption, or equipment malfunction. In manufacturing and R&D environments, this metric is crucial for maintaining operational continuity and ensuring that valuable sensor data, production metrics, and experimental results are preserved even during unexpected system outages. The data loss window directly impacts predictive maintenance capabilities, quality control processes, and regulatory compliance requirements, making it a fundamental consideration in industrial data architecture design and real-time analytics system implementation.
Core Components and Factors
Several technical factors determine the duration of a data loss window in industrial systems:
- Replication Frequency - How often data is synchronized between primary and backup systems
- Write-Ahead Logging - The mechanism used to record data changes before they are committed to permanent storage
- Backup Schedules - The timing and frequency of automated data backup operations
- Network Latency - Communication delays between distributed system components
- Buffer Management - The capacity and flush frequency of data buffers in memory before persistence
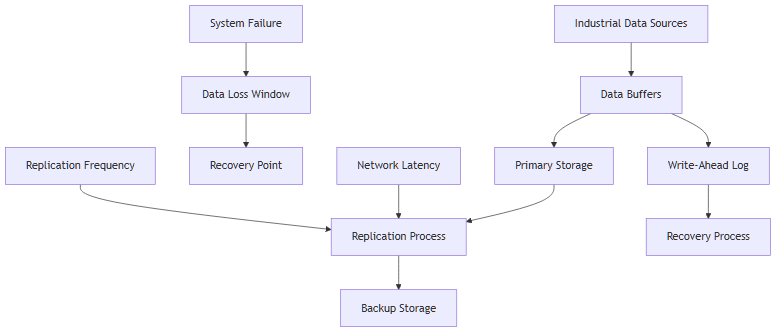
Applications and Use Cases
Manufacturing Operations
In production environments, data loss windows directly impact the ability to track product quality, monitor equipment performance, and maintain regulatory compliance. Critical production data must be preserved to support traceability requirements and quality investigations.
Industrial R&D
Research and development activities generate valuable experimental data that cannot be recreated. Minimizing data loss windows ensures that simulation results, test measurements, and prototype performance data are preserved for analysis and future reference.
Process Control Systems
Real-time control systems require minimal data loss windows to maintain accurate process history for optimization algorithms and safety systems. Extended data loss can compromise process stability and quality control.
Tolerance Requirements by Industry
Different industrial sectors have varying tolerance levels for data loss windows:
- Automotive Manufacturing - Seconds to minutes for production line data
- Chemical Processing - Milliseconds to seconds for safety-critical process data
- Aerospace Testing - Near-zero tolerance for flight test and certification data
- Pharmaceutical Manufacturing - Strict preservation requirements for regulatory compliance
- Energy Production - Minutes for operational data, seconds for safety systems
Minimization Strategies
Industrial organizations can implement several strategies to reduce data loss windows:
- Synchronous Replication - Ensures data is written to multiple locations simultaneously
- Distributed Storage Architecture - Spreads data across multiple physical locations to prevent single points of failure
- Change Data Capture - Continuously tracks and replicates data changes as they occur
- High-Frequency Backups - Increases backup frequency to reduce potential data loss
- Local Buffering - Implements edge-level data storage to maintain data during network outages
Performance Considerations
Reducing data loss windows often involves trade-offs with system performance:
- Latency Impact - Synchronous replication can increase write latency
- Network Bandwidth - Frequent replication consumes network resources
- Storage Costs - Multiple copies of data increase storage requirements
- Processing Overhead - Continuous backup operations consume computational resources
Related Concepts
Data loss windows are closely related to data retention policies for long-term data management, data provenance tracking for audit trails, and industrial data collection strategies. They also connect with time-series analysis requirements and data orchestration platforms that manage data flow and backup processes.
Understanding and optimizing data loss windows is essential for maintaining the integrity and availability of industrial data systems. Organizations must balance the need for minimal data loss with practical considerations of cost, performance, and system complexity to achieve optimal operational reliability.
What’s a Rich Text element?
The rich text element allows you to create and format headings, paragraphs, blockquotes, images, and video all in one place instead of having to add and format them individually. Just double-click and easily create content.
Static and dynamic content editing
A rich text element can be used with static or dynamic content. For static content, just drop it into any page and begin editing. For dynamic content, add a rich text field to any collection and then connect a rich text element to that field in the settings panel. Voila!
How to customize formatting for each rich text
Headings, paragraphs, blockquotes, figures, images, and figure captions can all be styled after a class is added to the rich text element using the "When inside of" nested selector system.