Anomaly Detection in Industrial Systems
Anomaly detection in industrial systems refers to the automated identification of unusual patterns, unexpected behavior, or deviations from normal operating conditions in manufacturing equipment, processes, and infrastructure. This technology is fundamental to modern industrial operations, enabling early detection of equipment failures, process inefficiencies, and safety hazards before they result in costly downtime or catastrophic events.
Understanding Industrial Anomaly Detection
Industrial anomaly detection systems continuously monitor sensor data from manufacturing equipment, comparing real-time measurements against established baselines of normal operation. Unlike traditional alert thresholding methods that rely on fixed limits, anomaly detection employs sophisticated algorithms to identify subtle deviations that may indicate emerging problems.
These systems excel at detecting complex failure modes that don't necessarily violate simple threshold limits but represent significant departures from normal operational patterns. For example, a gradual shift in vibration frequency patterns might indicate bearing wear long before temperature or amplitude thresholds are exceeded.
Types of Industrial Anomalies
Point Anomalies
Point anomalies are individual measurements that fall outside expected ranges for specific parameters. In industrial contexts, these might include:
- Sudden temperature spikes in rotating machinery
- Unexpected pressure drops in hydraulic systems
- Abnormal power consumption readings
Contextual Anomalies
Contextual anomalies are measurements that appear normal in isolation but are unusual within specific operational contexts. Examples include:
- High energy consumption during scheduled maintenance periods
- Temperature variations appropriate for summer conditions occurring in winter
- Production rates that match historical averages but are inappropriate for current product mix
Collective Anomalies
Collective anomalies involve groups of related measurements that collectively indicate developing issues. These patterns often signal complex failure modes:
- Correlated changes in multiple bearing temperatures suggesting lubrication problems
- Simultaneous variations in pressure, flow, and vibration indicating pump degradation
- Coordinated shifts in electrical parameters across multiple motor drives
Detection Methodologies
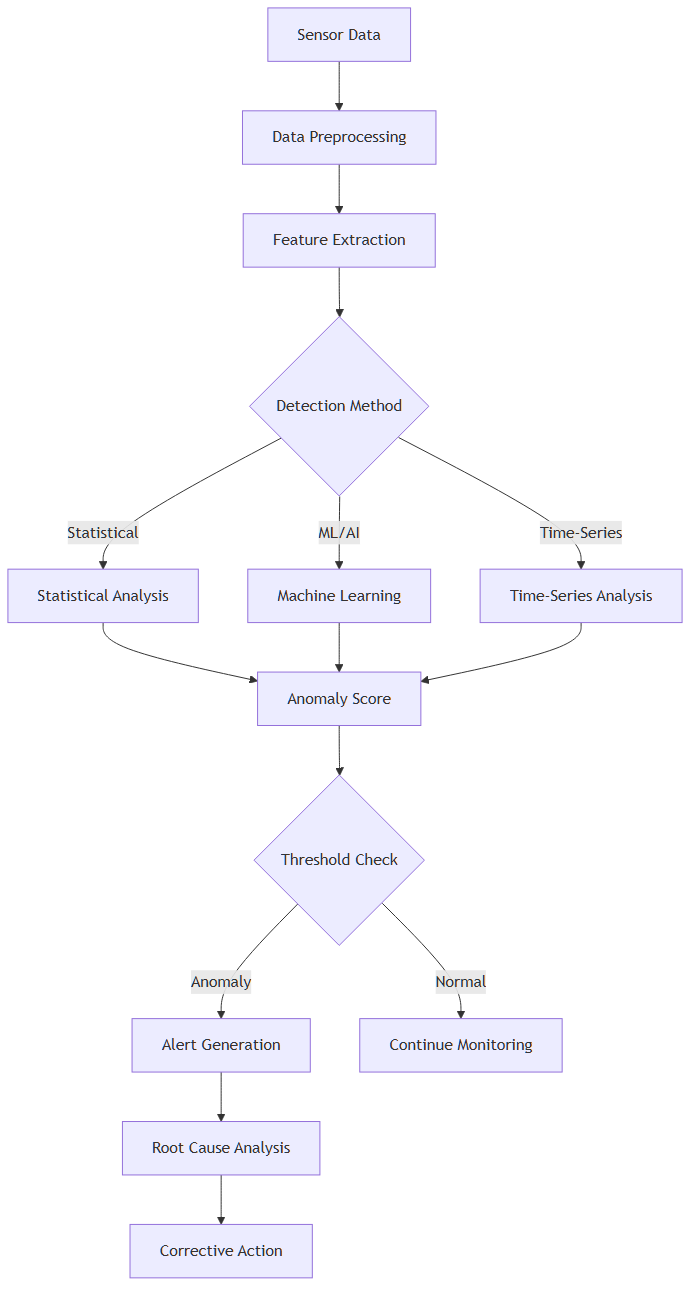
Statistical Methods
Statistical approaches establish normal operating ranges based on historical data distributions:
- Moving averages detect gradual shifts in process parameters
- Exponential smoothing identifies trends in noisy industrial data
- Multivariate statistical process control monitors multiple correlated parameters simultaneously
Machine Learning Approaches
Modern anomaly detection systems increasingly rely on machine learning techniques:
- Supervised learning uses labeled failure data to train classification models
- Unsupervised learning identifies patterns without prior knowledge of failure modes
- Deep learning automatically discovers complex feature relationships in high-dimensional sensor data
Time-Series Techniques
Time-series analysis methods are particularly valuable for industrial applications:
- Rolling window analysis detects local deviations from expected patterns
- Seasonal decomposition separates cyclical variations from genuine anomalies
- Change point detection identifies precise moments when operational regimes shift
Applications in Industrial Environments
Predictive Maintenance
Anomaly detection enables predictive maintenance strategies by identifying equipment degradation before failure occurs. This approach is particularly effective for:
- Rotating machinery monitoring through vibration analysis
- Thermal monitoring of electrical equipment
- Lubrication condition assessment in mechanical systems
Quality Control
Manufacturing quality control systems use anomaly detection to identify process variations that could affect product quality:
- Dimensional variations in machined parts
- Chemical composition deviations in process industries
- Surface finish irregularities in coating operations
Energy Optimization
Industrial energy management systems employ anomaly detection to identify inefficiencies:
- Unexpected increases in baseline power consumption
- Deviations from optimal operating points
- Equipment running outside designed efficiency curves
Safety Monitoring
Safety-critical applications require rapid detection of hazardous conditions:
- Gas leak detection in chemical plants
- Structural health monitoring in infrastructure
- Emergency shutdown system validation
Implementation in Model Based Systems Engineering
In Model Based Systems Engineering environments, anomaly detection algorithms are often developed using digital twins of industrial equipment. These virtual models enable:
- Simulation of failure modes for algorithm training
- Validation of detection performance under various operating conditions
- Optimization of detection parameters without risking actual equipment
Performance Considerations
Industrial anomaly detection systems must balance sensitivity with specificity to minimize both false alarms and missed detections. Key performance factors include:
- Detection Latency: Time between anomaly occurrence and detection
- False Positive Rate: Frequency of incorrect anomaly alerts
- False Negative Rate: Frequency of missed actual anomalies
- Computational Requirements: Processing power needed for real-time analysis
- Adaptability: System ability to learn from new operational patterns
Integration with Industrial IoT
Modern anomaly detection systems integrate seamlessly with Industrial Internet of Things (IIoT) architectures, leveraging:
- Edge computing for real-time processing
- Cloud analytics for complex pattern recognition
- Time series databases for historical analysis
- Machine learning pipelines for continuous model improvement
Anomaly detection in industrial systems represents a critical capability for maintaining operational excellence, safety, and efficiency in modern manufacturing environments. As industrial systems become increasingly complex and interconnected, these technologies will continue to evolve, providing ever more sophisticated capabilities for detecting and preventing operational problems.
What’s a Rich Text element?
The rich text element allows you to create and format headings, paragraphs, blockquotes, images, and video all in one place instead of having to add and format them individually. Just double-click and easily create content.
Static and dynamic content editing
A rich text element can be used with static or dynamic content. For static content, just drop it into any page and begin editing. For dynamic content, add a rich text field to any collection and then connect a rich text element to that field in the settings panel. Voila!
How to customize formatting for each rich text
Headings, paragraphs, blockquotes, figures, images, and figure captions can all be styled after a class is added to the rich text element using the "When inside of" nested selector system.